沈航 穆志国
摘要:在数字化测量系统中,测量软件直接以数学模型为评价依据,对于复杂零部件来说,往往特征种类繁杂、数目众多,在PC-DMIS中手动创建特征费时费力。本文介绍一种通过ASCII文件直接将特征数据导入到PC-DMIS软件,由PC-DMIS自动识别特征数据代替手动创建特征数据。该方法在多特征测量中具有显著的优势,实现从Modle到ASCII文件再到PC-DMIS的数据传输一体化。
关键词:ASCII文件 数据导入 快速读取 PC-DMIS
一. 引言
先进数字化技术有力的推动了产品设计、加工、装配技术的进步,为制造业的进一步发展奠定了坚实的基础。数字化潮流下,数字化检测技术也应运而生,产品检测由高精度通用测量设备代替了传统的检验器具,无论在精度、效率还是准确度上都有了长足的进展。关节臂测量机与PC-DMIS软件组成的测量系统是先进数字化测量系统的典型代表。
关节臂测量机测量精度高、适应范围广、便于携带、测量效率高,尤其是其具有高度柔性的关节可以使得我们在测量过程中采集到各种复杂区域的测量点。关节臂测量机广泛的应用于夹具调装、零件检测,并发挥着日益重要的作用。PC-DMIS软件操作方便、功能全面、计算准确度高,因此在汽车、航空等行业得到了广泛的应用。
PC-DMIS软件在进行尺寸评价、形状位置公差评价的时候,理论数据直接从数学模型上读取,测量数据由关节臂测量机采集。通过数学方法计算测量数据与理论数据的偏差,从而得出测量结果。PC-DMIS是以特征为要素进行几何量评价的,也就是说首先我们要在PC-DMIS中指定我们要测量的特征。通常在PC-DMIS中特征的指定是通过在导入的数学模型上手动选择来完成的,对于简单零件来说,特征数目较少手动选择可以胜任这项工作。对于复杂零件来说,存在数目众多的特征对象,如果将数模导入到PC-DMIS中手动选取特征不仅浪费了宝贵的测量时间,还会由于数目众多的特征导致特征选取的顺序混乱与差错。本文介绍一种通过ASCII文件的方式将特征直接导入到PC-DMIS中用于特征的读取代替传统的手动选取。基于ASCII文件,实现了从数模设计软件到PC-DMIS软件的数据交流,避免了手动选择可能出现的的潜在错误。大量实验表明,该种方法简洁明了、快速高效,完全满足使用要求。
二. 基于ASCII文件的PC-DMIS理论数据快速读取方法
2.1 PC-DMIS理论数据快速读取方法需求
关节臂测量系统中,几何量测量的核心就是准确获得几何特征的数据,运用科学的计算方法来评价测量数据。测量数据的评价直接以数模为依据,通过将测量值与理论值对比,得出测量结果。PC-DMIS中,测量数据评价是以“特征”为要素来进行的,也就是说结果评价是通过相关特征的理论/测量数据来进行的。从操作上来说 ,首先我们要在PC-DMIS中读取相关特征在数模上的坐标值作为结果评价的理论值,其次使用关节臂测量机在产品上测量相关特征获得其测量值,由PC-DMIS软件根据相关特征的理论值与测量值计算得出测量结果,数据关系如图1所示。
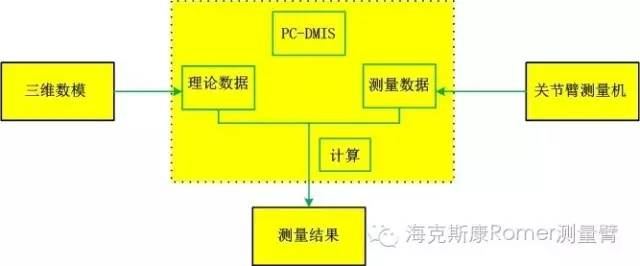
图1 关节臂系统数据关系
测量过程中建立零件坐标系之后,特征的理论数据是其在数模坐标系下的值,测量数据是测量仪器建立的零件坐标系下的值。也就是说,理论数据是直接从数学模型上获取的,与是否导入PC-DMIS、是否建立零件坐标系并无关系。该点表明从设计软件上直接获取数学模型相关特征的理论数据与导入PC-DMIS建立零件坐标系后手动选取特征,两种方法特征要素的理论值完全相同,大量实验也表明了这一点。该理论为我们将预先获取特征理论数据的ASCII文件并导入PC-DMIS以实现特征数据的快速读取提供了理论支持,如图2所示。
对于复杂零部件来说,在数学模型上手动选取大量的特征要素一方面占用了宝贵的测量工时,另一方面容易出错。如果我们能够在ASCII文件中定义相关特征的理论数据,使用ASCII文件直接将特征参数导入到PC-DMIS中完成特征理论数据的自动读取,一方面极大的缩短了特征选择的时间,避免了手动选择导致的错误还实现了从设计软件到测量软件数据的交流。
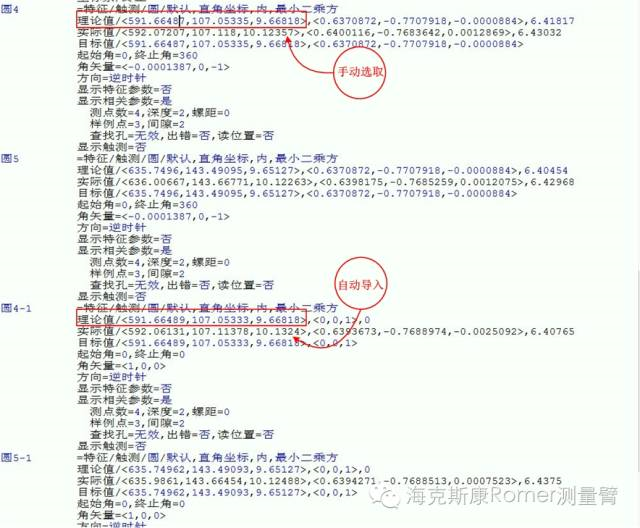
图2 两种方法读取理论值比较
2.2 PC-DMIS特征快速读取方法
特征快速读取方法实现了从设计软件到PC-DMIS的数据直接交流,节省了大量的手动操作,数据交流的桥梁是ASCII文件。因此,特征快速读取方法的核心就是如何快速的从设计软件获取理论数据,如何在ASCII文件中定义理论数据的格式,如何引导PC-DMIS软件按照该格式读取预先写入ASCII文件的理论数据。本文以CATIA软件作为设计软件,简要介绍设计数据的快速获取、ASCII文件的预定义格式读取等方法。
2.2.1 设计软件理论数据的获取
以CATIA为设计软件,可以方便的将相关特征要素的理论数据导出为EXCEL或者ASCII文件,为我们下一步工作奠定了基础。从CATIA软件导出相关特征要素的方法如图3所示。
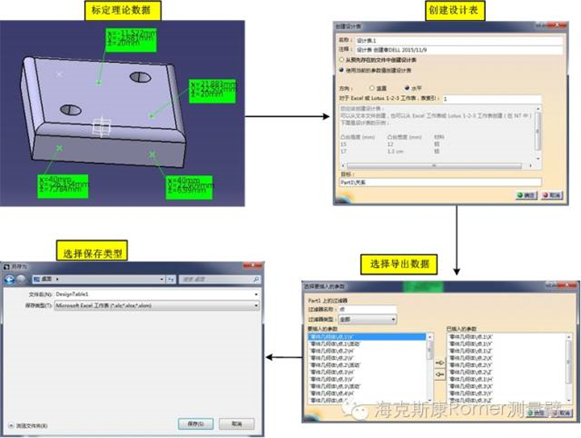
图3 理论数据的导出
2.2.2 ASCII文件的制作
获得理论数据之后,我们在ASCII文件中以恰当的格式来定义相关特征。在ASCII文件中定义特征数据时一定要注意理论数据的书写顺序,尤其是不同数据之间的分隔符,分隔符是我们在导入PC-DMIS时PC-DMIS能否正确识别理论数据的关键点,如图4所示。
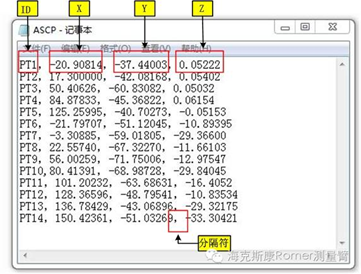
图4 ASC文件
2.2.3 PC-DMIS从ASCII文件快速读取理论数据
在ASCII文件中定义完特征的理论数据之后,就可以将其导入到PC-DMIS中了。ASCII文件导入PC-DMIS,利用PC-DMIS软件自带的导入功能,按照数据导入向导根据在ASCII文件中预先定义的理论数据格式逐步设置,最终完成理论数据的导入。
首先选择定义了特征理论数据的ASCII文件,为保证ASCII文件的成功导入根据软件系统本身的规则,建议将ASCII文件放置在“桌面”上,不要放置在文件夹里面;
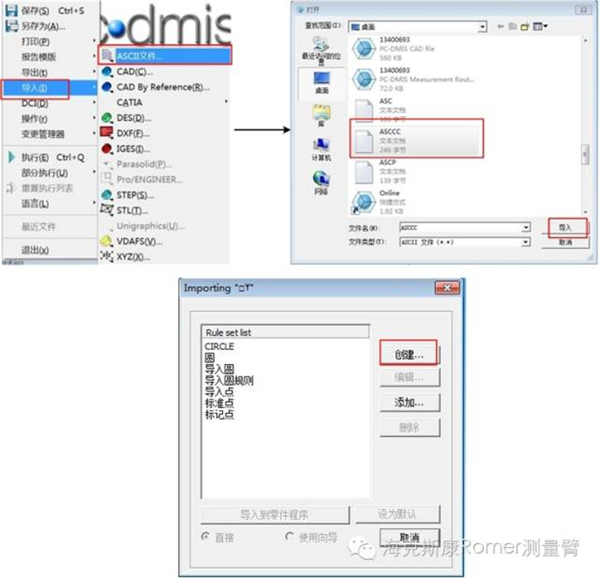
图5 选择ASCII文件
选择ASCII文件之后,进入PC-DMIS识别ASCII数据阶段。在这一阶段要按照在ASCII文件中预先定义的理论数据格式,正确的选择向导中的条目,完成理论数据的导入。
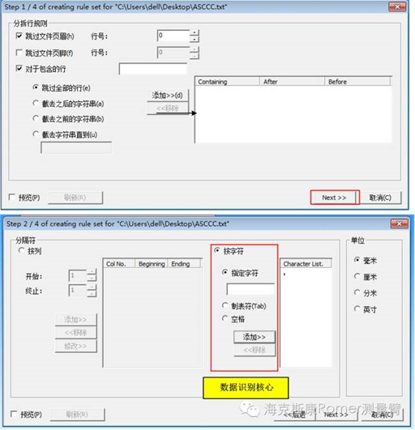
图6 数据点的提取
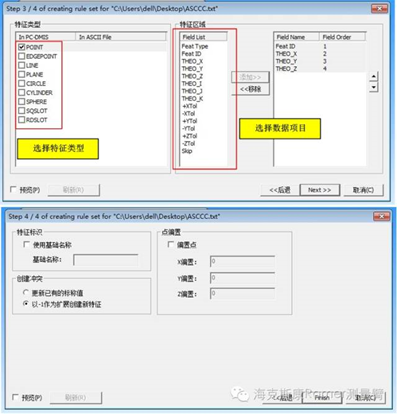
图7 数据项目的设定
完成理论数据的识别之后,也就是建立了一个数据导入规则。凡是符合这个数据导入规则的ASCII文件都可以直接使用这个数据导入规则而不需要重新建立数据导入规则。最终完成理论数据的导入,在编辑窗口以及图形显示窗口会立即显示导入的特征类型以及理论数据。
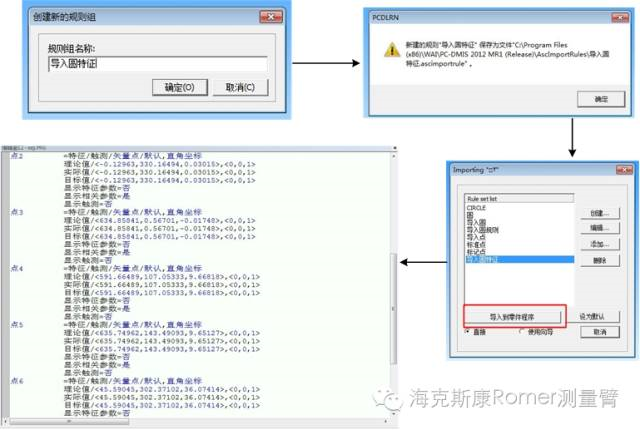
图8 导入到PC-DMIS
经过上述方法,成功的将从设计软件中导出的相关特征理论数据以ASCII文件为桥梁,导入到PC-DMIS中实现了理论数据的自动读取。多次试验结果表明,该种方法操作简便、快速高效,所导入的理论数据可满足坐标系建立、特征测量的理论数据需求。与在数模上手动选取相比具有明显的优势,完全满足测量任务的需求。
三. 基于ASCII文件的PC-DMIS特征数据快速导入方法在某叶片测量中的应用
3.1 某叶片测量要求
叶片是发动机的关键组成部分,需求数量巨大,精度要求高。能否准确的对叶片进行测量,包括采用合适的测量设备、合理的测量方法、准确的数据计算是关乎叶片生产、交付的重要因素。叶片属于自由曲面,型面复杂,测量较为困难,尤其对于复合式叶片来说还面临着测量空间的限制,给测量工作进一步带来了难度。本文所要测量的叶片属于开式复合叶片,其测量空间满足了关节臂测量机测头的活动要求,如图9所示。
叶片型面几何形状精度由三个因素构成,即叶片型面轮廓度误差、弯曲变形误差、扭转变形误差。叶片型面截面线轮廓度控制叶片截面形状精度;叶片截面积叠点的位置度控制叶片的弯曲变形;叶片扭转变形误差控制叶片扭转变形。目前图纸以多个截面线轮廓度控制型面轮廓度。
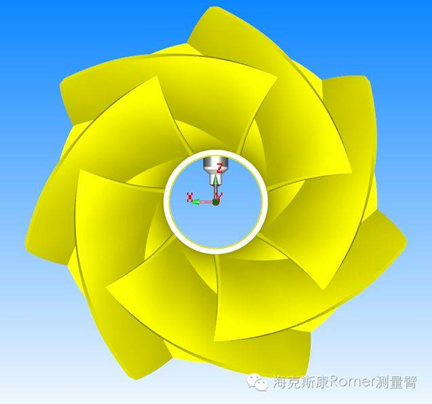
图9 某型叶片
3.2某型叶片测量过程
按照叶片测量要求,采用关节臂测量机完成该叶片的测量工作。具体过程分为测量路径规划,测量点的采集与数据处理三个部分。
3.2.1测量路径规划
由于叶片测量是由多个截面的线轮廓度来控制型面轮廓度,因此只需要在叶片上采集几个型面的测量点即可。按照目前叶片的主流测量方法,采用等高法来规划整个叶片的测量路径。
首先在CATIA软件中完成测量路径的规划即叶片截面的确定,根据叶片不同区域的曲率在截面上分配不同的点。然后将测量点导出,转换为预定义格式的ASCII文件。按照PC-DMIS特征数据快速导入方法,将ASCII文件导入到PC-DMIS软件中作为测头路径的引导,最终完成测量数据的采集,测量路径与测量点如图10所示。
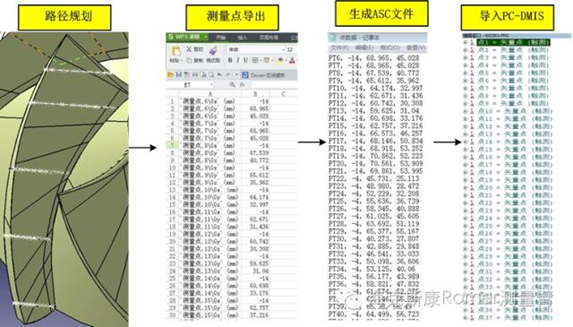
图10 测量路径
3.2.2坐标系的建立
根据复合叶片设计基准,使用3-2-1法建立坐标系,具体如图11所示。
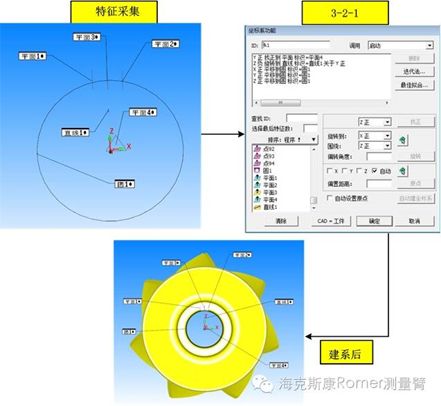
图11 坐标系建立
3.2.3测量数据的采集
(1)使用关节臂测量机,以导入PC-DMIS的测量点为测头的轨迹引导点,打开自动测量点模式,按照蜂鸣声的提示完成测量点的采集,最终实现手动测量完成各个截面数据的采集,克服了手动测量很难实现测量点在同一截面的问题。
(2)使用关节臂自带的激光扫描头,配合Geomagic Control 完成叶片扫描。利用该软件的“位置集”功能,将ASCII文件中的测量点信息导入到软件中,直接实现对指定点偏差的分析,而不需要手动选取偏差点。以ASCII文件中的测量点信息作为“位置集”源文件导入Geomagic Control 软件中对于批量零件测量来说尤为方便,使用“位置集”可以实现对同一批次不同零件相同位置测量点的快速评价,如图12所示。
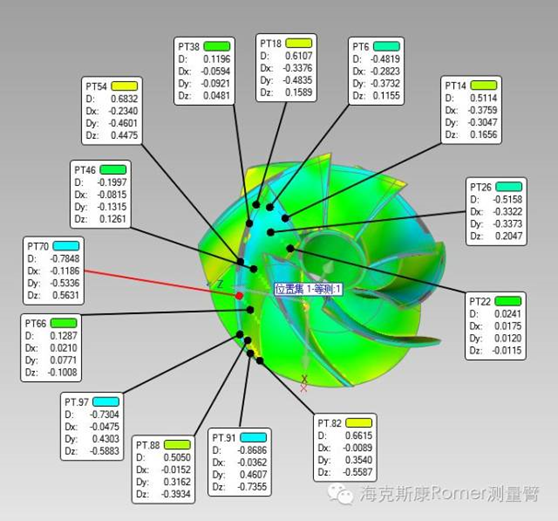
图12 测量点偏差
(3)使用桥式机对叶片进行测量时,可以直接使用通过ASCII文件导入的测量点作为测头轨迹的引导点,给程序的编制带来极大的方便。
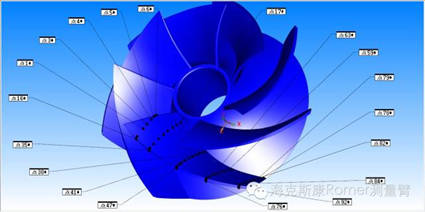
图13 导入PC-DMIS中的测量点
尤其在使用关机臂进行夹具安装、定检的时候,通常夹具上有众多的“圆特征”,这时候利用ASCII文件导入“圆特征”的参数,就可以发挥出这种方法的优势,大大缩短在PC-DMIS上的操作时间,使得我们专注于关节臂测量机本身。
3.2.4测量数据评价
完成测量数据采集后,部分截面上的测量点偏差如图14所示。
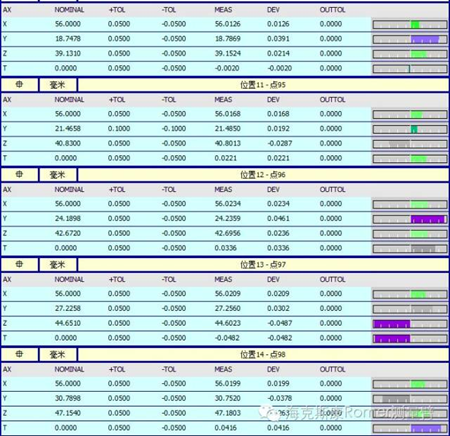
图14 部分测量点偏差
四. 结语
本文重点介绍了在ASCII文件中以一定的格式预先定义测量特征的理论数据,通过PC-DMIS软件中的“导入”功能,实现了大批量、多特征类型、复杂数据项目的理论数据导入,实现了在PC-DMIS软件中的理论数据快速读取。
PC-DMIS软件在形位公差测量方面具有显着的优势,而形位公差的测量是以具体的特征(点特征、线面特征、体特征)为依据和手段的。本文介绍的PC-DMIS特征理论数据快速读取方法为在PC-DMIS中指定特征的理论数据提供了一种新的方法,该方法不需要借助其他软件或者外联程序,仅仅依靠PC-DMIS软件自身提供的“导入”功能和最基本的ASCII文件即可完成该工作。实践证明,这种方法是可行的、高效的。
五. 参考文献
[1] PC-DMIS For Arm 培训手册
[2]朱立强,杜砾.三坐标测量软件(PC-DMIS)的二次开发应用.中国会议,2013年
[3]邓明霞,孙国辉等.应用PC-DMIS扫描测量涡轮盘叶片[J].航天制造技术,2009年
[4]原小敏.基于PC-DMIS软件的脱机编程方法及其应用[J].科技资讯,2014,18,29-31
[5]周敏,徐旋波.基于PC-DMIS和UG的反求工程技术[J].现代制造工程,2008,11,38-40