一汽大众 柳强
[摘要]:三坐标测量机是数字化制造中的关键技术。其准确、快速、灵活的测量方式,不断的推动着整车制造工厂质量分析工作的发展。近年来便携式三坐标测量机领域,取得了很多新的成果与突破。如:开机时无需归零操作,可以实现测头间热插拔的“绝对臂技术”,可以实现多台关节臂同一坐标系下测量的“Grid-lok”技术等,实现了便携式三坐标测量机在汽车制造业,质量分析领域内从小型零部件到商品车整车的全覆盖式测量;
一汽-大众汽车有限公司于1991年2月6日成立,一直以来一汽-大众汽车有限公司都致力于打造中国最优秀的汽车合资企业。随着公司产量的不断提升,对整车匹配质量问题分析工作的要求越来越高。便携式三坐标测量机的引入加快了匹配质量问题分析的速度,提高了匹配质量问题分析的质量。
本文将着重讲解便携式三坐标测量机在一汽-大众整车匹配质量问题分析中的应用。
[关键词]:发展、意义、匹配分析应用、位置偏差
引言
三坐标测量机作为现代大型精密测量仪器已有40多年的历史,20世纪60年代以来,随着现代化汽车制造行业、机械制造行业、航空航天行业等的兴起,各种复杂零件的研制急需先进的检测仪器对其检测;同时,随着人们对产品质量重视程度的不断提升,对生产制造过程中质量问题分析解决的相关要求也越来越高,移动便携式三坐标测量机的引入,使三坐标测量机的应用领域愈加宽广,己经越来越显示出它的重要性和广阔的发展前景。
一、便携式三坐标测量机对过程质量分析的意义
三坐标测量机是测量和获得尺寸数据的最有效的方法之一,因为它可以代替多种表面测量工具及昂贵的组合量规,并把复杂的测量任务所需时间从小时减少到分钟。这对过程质量问题分析会带来极大的便利。三坐标测量机的功能是快速准确地评价尺寸数据,及时为质量分析人员提供详实、有用的尺寸变化信息,这与其它的手动测量设备有很大的区别。将被测物体置于三坐标测量空间,导入数模按照图纸上规定的RPS点建立坐标系后,即可获得被测物体上各测点的准确坐标位置和偏差量,第一时间将相关信息提供给质量分析人员。有了三坐标测量机:
1)防止了不同质量分析人员手动测量的误差,统一了测量标准稳定了测量质量。
2)加快了质量问题分析的速度。在解决突发质量问题时,利用移动三坐标测量机可以实现缺陷问题现场测量,满足了质量问题分析对时间的苛刻要求。
3)可以对生产过程中的夹辅具进行“预防性”现场测量,在质量问题发生前提出相关预警。
4)逆向工程的需要,在日常生产中需要有配合装配及检验的快速样板,以往这样的需求需要专业公司进行制作,价格昂贵不说,制作周期漫长,不能满足生产需要。有了移动三坐标测量机后,可以利用三维激光扫描头进行所需样板的逆袭扫描,根据这些数据编制加工的程序。
综上所述,便携式三坐标测量机的出现,极大的方便了整车匹配质量问题分析工作,使之后的质量问题改进有据可依。
二、便携式移动三坐标测量机的应用
便携式三坐标测量是车间现场理想的三维尺寸测量工具,能够完成狭小空间内的高精度测量。以高精度和高效率的绝对优势代替传统手动测量工具,作为固定式三坐标的完美补充,完成车间的多种测量任务,使快速的质量问题现场测量成为可能。便携式三坐标测量机的种类和形式有多种,常见的有关节臂式测量机、激光跟踪仪、激光扫描仪等。
2.1在日常质量问题分析中的应用
在整车制造厂中,每日会面临各种各样的匹配分析类质量问题。以往只能通过塞尺、卡尺及对比安装实验来分析导致问题的原因。由于每个人的操作手法不同,所以得到的数据缺乏统一的标准,有时甚至会出现每个人测量结果都不同的情况。在有了便携式移动三坐标测量机后,这种情况得到了明显的改善。通过利用图纸上的RPS点建立统一的坐标系,可以实现不同人测量,所得数据相一致的效果。为质量问题分析提供了统一的标准。下面以典型案例讲述便携式三坐标测量机在日常质量问题分析中的作用。
质量问题描述:某某 车型左侧大灯与保险杠 X向平度不好(目视保险杠低于大灯)。
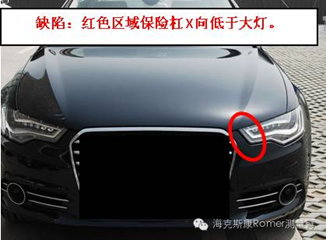
图1 缺陷问题描述
通过测量解决的过程描述
1) 将缺陷车辆开至测量分析间,使用四个千斤顶将缺陷车辆支起进行妥善的固定(车辆的减震系统会造成不稳定,影响测量结果的准确性)。将便携式车辆机固定于车辆正前方,连接好数据线及电源线,并与配套移动工作站联通,做好测量前期准备工作。
2) 查找两侧翼子板单件图纸上RPS点信息及近期批量监控测量信息(对比单件RPS建系点稳定性),下载数模文件,利用迭代法建立缺陷车辆前端局部坐标系(如图2)。
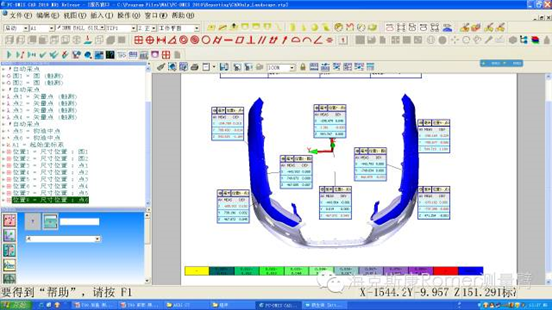
注:取点1、点3、点5(点2与点4中点)定位Z向,取圆1、圆2定位X向,取点6(圆1与圆2中点)定位Y向
图2 建系点信息描述
采用两侧翼子板建立坐标系的原因是:此次缺陷的相关零件均是以翼子板为基础进行装配的。以两侧翼子板建系可以很好的模拟零件装配状态,反应实际的尺寸偏差形式。在这里所选用的建系点都是装配调整中的尺寸控制点,之所以选择矢量点建系,也是为了充分的模拟实际零件间的装配状态。而取对中点则在于考虑整体的平均偏差趋势。
1) 建立坐标系后,使用3MM测量头进行测量操作,首先对建系的相关点位进行探测,确定坐标系建立的准确性。而后对缺陷区域进行探测,首先探测缺陷左侧大灯,得出相关测量结果(如图3)
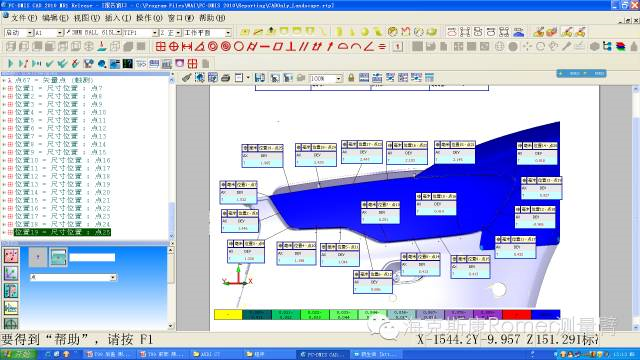
图3 左侧缺陷大灯测量数据
对于缺陷大灯的测量,采用的曲面点方式进行,我们这里叫做POS点(垂直于法线上的点),这样可以很好的评价缺陷区域间隙、面差(所要测量的点不在单纯的某一方向上)。通过测量发现,左侧大灯在缺陷区域(图3 红圈处)发生了向车身前部1.3~1.5MM的偏差。证明左前大灯在缺陷部位发生向前的偏移,对缺陷有不利的影响。
接下来用同样的方法对缺陷车辆保险杠进行测量(见图4)
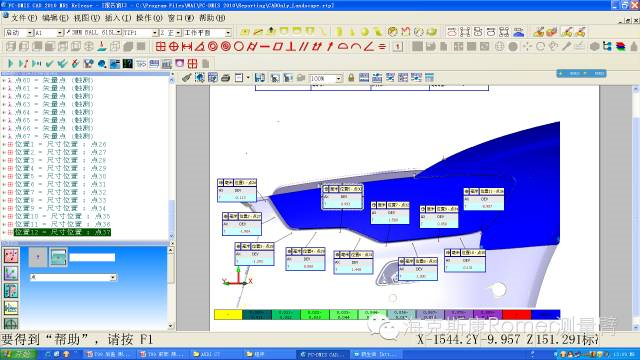
图4 左侧缺陷保险杠测量数据
通过对左侧保险杠的测量可以发现:在缺陷区域保险杠发生向车身后部的偏差(最大2.1MM),与大灯发生偏差方向正好相反,加剧了缺陷的状况同样对缺陷有不利的影响。
接下来拆下缺陷大灯、保险杠等相关件,对固定大灯的支架进行测量(见图5)
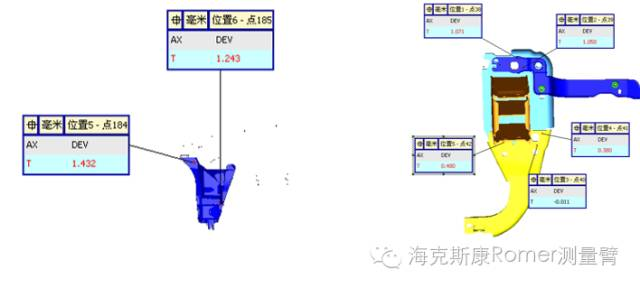
图5 大灯固定支架及支架固定梁测量数据
通过测量数据可以看到,大灯固定支架(图5左侧)发生向前的偏差,会导致大灯随之发生向前的偏差,而支架固定梁同样发生向前的偏差,证明支架是随梁发生向前的偏差。最终证明左侧大灯发生向前偏差是由左侧纵梁偏差导致的。
接下来对缺陷车辆前盖进行测量(见图6)
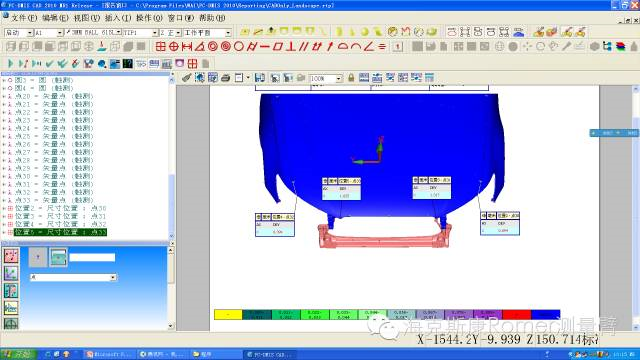
通过测量发现:前盖与前杠匹配处(图中红圈)发生向后的偏差(注意:此处取的是前盖X向偏差,按照整车坐标系原理“前负后正、左负有正、上正下负”则为发生向后的偏差),由于前杠 X向是随前盖进行调整的,所以证明前杠是随前盖发生向后的偏差。
最终通过完善测量步骤,得出缺陷问题测量角度上的分析结论:
1. 左前纵梁发生向前的偏差,导致左前大灯随之发生向前的偏差,对缺陷不利。
2. 前杠随前盖发生向后的偏差,对缺陷不利。
2.2 在突发质量问题分析中的应用
由于整车生产需要使用各种零部件,各种零部件又是由不同配套厂家生产的。所以在日常生产中经常会遇到由于外协厂家零件尺寸不稳定,导致的突发性质量问题。为了保证正常生产顺利进行,必须在第一时间排查出导致质量问题发生的零部件。依靠常规测量方式进行,往往会耽误许多时间,影响改进工作的进行。在有了便携式移动测量机后,情况得到很大幅度的缓解。下面以真实案例进行说明:
质量问题描述:某某 车型后杠骨架安装不上,导致生产线停台。
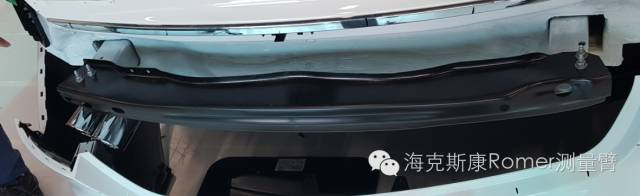
图1 缺陷问题描述
1) 由于是突发质量问题,所以将便携式三坐标测量机运至生产线现场进行测量。将缺陷后杠骨架利用装配夹具进行定位(由于涉密故图片不能展示)。根据零件匹配关系要求建立坐标系(见图2)
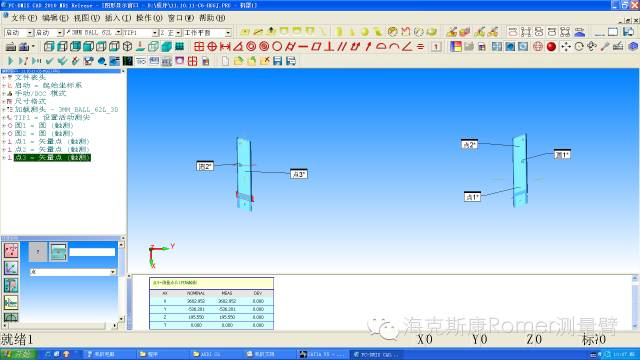
注:此次测量采用点1~点3定位Z方向,圆1与圆2定位X方向,圆1定位Y
图2 建系点信息描述
2) 建立坐标系后,使用3MM测量头进行测量操作,首先对建系的相关点位进行探测,确定坐标系建立的准确性。而后对缺陷区域进行探测,由于后杠骨架是通过前端固定钉孔与车身进行装配的,故决定对固定钉孔位置尺寸进行测量(如图3)
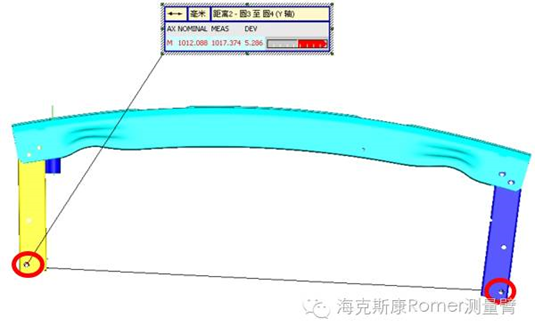
图3 测量后杠固定固定钉孔
测量完固定孔后,利用构造直线工具,以左、右固定孔圆心构造一条直线,求出构造直线的长度偏差为5.28MM,证明缺陷是由于后杠骨架固定钉孔位置偏差所导致。及时将相关测量结果通知外保同事对缺陷问题进行促进。并通知生产线对当天批次缺陷件进行封存。
利用便携式三坐标测量机,使整个缺陷问题在2小时内得到妥善解决,防止了长时间的停台对生产造成的影响。
2.3 在预防性工作领域中的应用
白车身质量稳定的基础是焊装车间的夹辅具定位系统,夹辅具定位系统由各种定位销、定位块及相应的加紧机构组成。这套加紧定位系统的稳定性对白车身质量的影响巨大。利用生产间歇时间及时的对其进行预防性的尺寸监控,可以在白车身质量缺陷发生前给予预警。可以更好的保证白车身质量的稳定性。而进行这种尺寸监控,势必用到便携式三坐标测量机。下面简要说明该领域的测量流程:
首先与懂得焊装夹辅具工作原理及白车身焊接整体流程的同事充分沟通,对焊装车间现有的夹辅具进行重要程度划分,找出会影响白车身质量稳定的重点工位。利用生产间歇时间对选定工位进行实地踏查,评价是否可以进行测量,并确定使用何种便携式三坐标测量设备(如图1)。
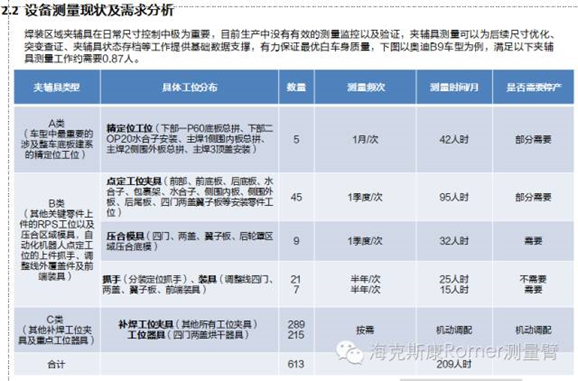
图1 选定测量工位
在确定了需要进行监控式测量的工位后(主要是一些点定工位),根据日常生产安排,确定进行测量的时间点。与此同时向夹辅具责任部门索要所需测量工位,工装夹具的图纸与数模(评价特型定位块需要使用数模)文件,为后续的测量工作做准备(如图2)
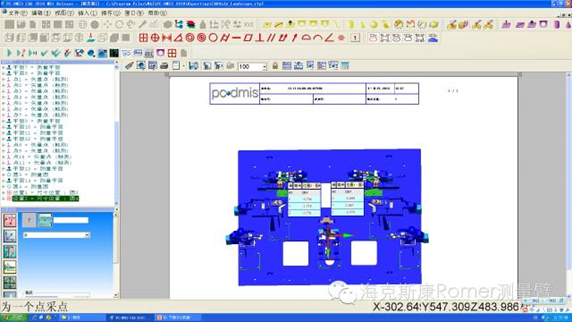
图2 准备好相关图纸与数据
做好测量准备后,就可以按计划对所需监控的工位进行测量。对有图纸和数模的工位,可以使用迭代法建立坐标系(如图3左)。对没有图纸和数模的工位,只能通过利用BAIS板上的定位孔,自行建立坐标系测量(采用3.2.1法建立坐标系,见图3右),但需要记住建系所用定位孔,以便在下次测量时按照相同定位孔,使用相同建系方法建系,评价两次测量间的尺寸偏差。
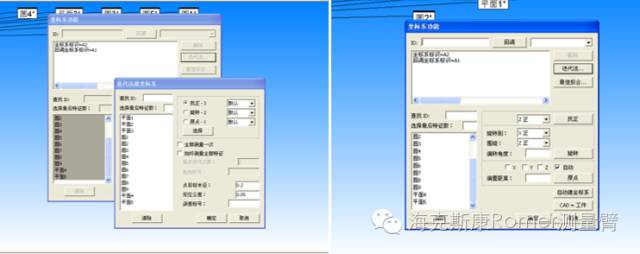
图3 两种不同的建系方法(左为“迭代法”右为“3.2.1法”)
最后将测量数据进行存档,以便日后再次测量时对比观察尺寸变化趋势,对白车身质量变化提出预警性建议。
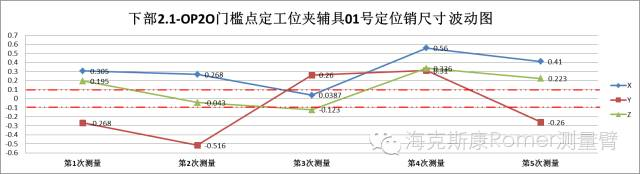
图4 通过多轮监控式测量,形成定位销、孔的尺寸波动图
2.4 在逆向制作领域中的应用
在日常生产中需要使用到配合装配及检验的快速样板,以往这样的需求需要专业公司进行设计、制作,价格昂贵不说,制作周期漫长,不能满足生产需要。有了便携式移动三坐标测量机后,可以利用三维激光扫描头对所需样板进行扫描,根据扫描得出的点云数据利用逆向软件 Geomagic Design X 进行逆向复制,并将复制出的数据提供给加工制作部门进行逆向制作。下面简要介绍下具体工作流程:
案例:利用逆向扫描制作检验压块
某某车型车门密封条压块损坏,需要制作新的检验压块,由于此压块无图纸及数模,故需要利用激光扫描头对破损的压块进行扫描,并利用逆向软件修复损坏部位。然后将最终的数据交给制造部门利用3D打印机进行后续制作(如图1)。
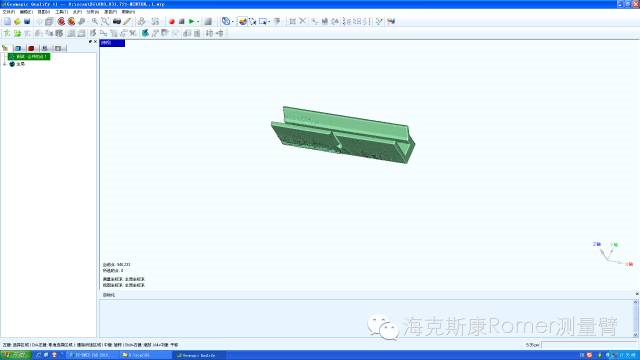
图1 使用激光扫描头扫描的压块点云文件
通过利用逆向扫描制作检验压块,省去了重新订购的漫长等待和大量的资金。极大的方便了日常工作的进行。
三. 结论
随着移动便携式测量机及PC-DMIS测量软件的不断进化,对我们整车制造企业在整车质量问题分析中带来了极大的便利。使我们由过去那种“盲人摸象”式的分析工作方式,发展到了有准确测量数据做支持、有完善解决方案做后盾,可以实现提前预警潜在质量风险的数字化分析时代。在此要对以海克斯康为代表的,先进的测量技术致以真切的感谢。