作者:何新毅 张庭芳 张超敏 盛威
本文转自e-works网站
运用逆向设计的原理,以保时捷汽车模型车身为研究对象,利用激光扫描获得车身表面的点云数据;用Geomagic Wrap(原Studio)软件对点云数据进行体外孤点、噪声点的去除以及点云拼接与对齐;然后用软件进行由点—线—面的曲面重构过程,并对曲面进行连续性和光顺性分析,得到质量良好的汽车车身CAD模型,完成了逆向工程在车身设计中的应用初步研究。
逆向工程(又称反求工程),是一种产品设计技术再现过程,即对一项目标产品进行逆向分析及研究,从而演绎并得出该产品的处理流程、组织结构、功能特性及技术规格等设计要素,以制作出功能相近,但又不完全一样的产品。逆向工程的应用范围遍及大多数行业,从汽车、航空航天、艺术与科学到医疗等。目前国内外有关逆向工程的研究方向主要集中在几何外形的逆向,即重建产品实物的CAD模型,称为“实物逆向工程”。逆向工程系统主要包括3个方面:实物几何外形的数字化、CAD模型建立、产品的制造。
现代车身设计采用的都是传统的设计方法,然而,汽车外形结构复杂,曲面很多,要用一般的机械图纸把它完全表达出来需要大量的人力物力,相当浪费时间。不过,在逆向工程设计方法引进到汽车车身设计时,它改变了以前的设计理念,缩短了设计开发周期,获得高质量的车身结构。逆向工程的研究日益引人注目,在数据处理、曲面拟合、几何特征识别和坐标测量机的研究上已经取得了很大的成就。但是,在实际应用中,整个过程仍然不能完全保证曲面的光顺性。针对这些特点,本文研究的关键有:1)曲面数据的获取以及后续的数据处理等;2)车身曲面的重构技术及质量检测等。
1. 点云数据的采集与处理
1.1 点云数据的采集
点云数据的采集使用的仪器是智泰精密仪器有限公司的3D Family激光抄数机,如图1所示。
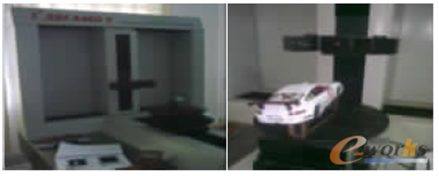
图1 测量设备
为了获得质量较好的点云数据,首先进行一些前期处理,如确定模型参考位置、表面喷涂显像溶剂及软件的校核等。汽车模型由前、后、上、左、右侧面组成,由于不能一次性测量,因此要分别测量各个表面,对于侧面,只需要测量一侧就行,因为汽车是左右对称的产品,可以利用软件镜像。图2、图3为采集的未处理的车身点云数据。
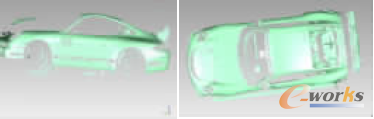
图2 车身侧面和顶部的点云数据
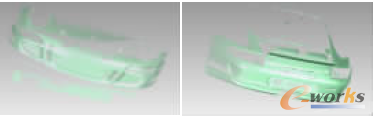
图3 车身前部和尾部的点云数据
1.2 点云数据的处理
在测量点云的时候,难免会有一些外界因素影响点云质量,如设备的震动、温度、湿度等,而且点云不能一次性测量,需要分为几步,最后把几部分拼接起来,这就要求在进行模型建立之前对点云进行处理。主要分为以下几步:体外孤点、噪声点的去除、点云拼接与对齐。利用Geomagic Wrap(原Studio)软件进行处理,处理拼接后的整车点云如图4所示。
图4 拼接后的整车
2. 车身模型曲面重构
在逆向工程中,曲面重构有2种方法:一是直接由点云生成面;二是遵循由点—线—面的过程。第1种方法要求点云数据质量足够好,这样生成的曲面质量才会满足要求,它遵循点—多边形—曲面几个阶段,运用的是Geomagic Wrap(原Studio)软件;第2种方法是传统的方法,可以处理各种点云数据,得到的曲面精度也很高。本文主要采用的是第2种方法。数据处理主要有以下3个过程:点云数据处理、曲线处理、曲面处理。由于在Geomagic Wrap(原Studio)中已经对点云数据进行了处理,可以直接进行后面2个步骤。
2.1 点云直接生成曲面
所谓的直接生成曲面是指不需要构线,对点云进行处理就可以生成曲面。直接生成的NURBS曲面可以直接导入到CAD系统中进行下一步的处理,可以输出很多种格式,如IGES、STEP等。图5为生成的NURBS曲面。
图5 NURBS曲面
2.2 由点、线、面的重构过程
点—线—面过程主要是利用3D曲线、3点圆弧构建曲线,然后利用扫掠、桥接、倒圆角等命令对曲面进行处理。
1)创建车身曲线。由于车身是对称模型,因此创建曲线之前需要截取一部分点云,最后通过镜像得到整车模型。创建曲线是在已有的点云基础上截取部分点云,然后由截取的点云生成曲线,最后调整曲线的控制点来控制精度,让其和点云的误差最小。生成的曲线要尽可能简单,能够反映曲面的大致形状,这样才能保证重构后的曲面有足够的光顺性,同时误差也较小。图6为截取的车身侧面点云和由截取点云构成的线。
图6 截取的点云和构成的线
2)创建车身曲面。创建曲面通常光滑和精确是不能同时兼顾的,只能居其中或者择其一。为了控制误差,通常利用调节控制点来控制曲面与原始点云的距离,这种方法通常是手动调节,因此也是存在一定误差,但是也基本可以满足工业要求。图7为车身侧面控制点模型,图8为重构的车身侧面曲面与原始点云之间的误差。
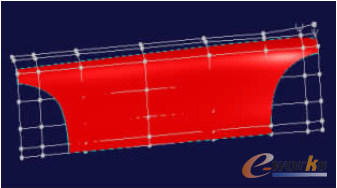
图7 车身侧面控制点
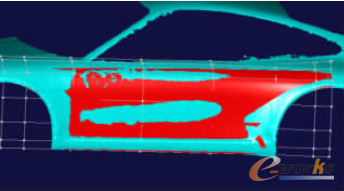
图8 车身侧面与原始点云误差
由图8可以看出:车身侧面原始点云(蓝色区域)和重构的曲面(红色区域)分布比较均匀,这样就可以大致确保曲面与点云的误差了。如果出现大面积红色或者蓝色区域,则说明重构的曲面与原始点云误差较大,不能满足需求。这种方法是通过调节控制点来控制误差,本文车身逆向设计主要是利用这种方法。图9为通过这种方法重构的引擎盖和车身顶部曲面。
图9 引擎盖和车身顶部
2.3 各个曲面间的处理
各部分曲面创建好了之后,需要对曲面进行倒圆角、修剪、桥接、缝合等操作,以得到连续性的曲面。倒圆角是一种基本的曲面间处理方式,圆角过渡不仅避免了应力集中,提高了强度,而且直接影响产品的美观程度。图10为车尾曲面间倒圆角前后效果图。
图10 车尾曲面倒圆角前后效果
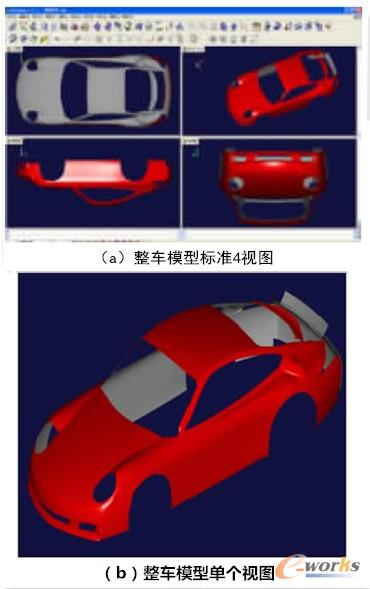
图11 整车车身模型
3 车身曲面质量评估
3.1 曲面连续性分析
对于车身而言,连续性就是指曲面间曲率均匀过渡、无坏点。曲面的连续性大致包括以下4个方面:位置连续(G0)、切线连续(G1)、曲率连续(G2)、曲率相切连续(G3)。一般情况下,只要满足切线连续就可以,基本可以满足工业上需求。在汽车行业有一个名词:A面。所谓A面就是指必须满足相邻曲面间间隙在0.005mm以下,切率改变在0.16°以下,曲率改变在0.005°以下的曲面。一般通过曲率梳可以判断曲面的连续性,曲率梳相邻曲率针长度和方向反应曲面的曲率值和曲率方向。检查U、V方向的曲率梳得到车尾和车头的分析结果,如图12所示。
图12 车尾和车头处连续性分析结果
图12中显示车尾和车头处多个曲面间连续性较好。
3.2 曲面光顺性分析
曲面光顺性分析准则是光顺分析的依据。曲面光顺准则为:曲面的U、V等参数线分别平行于U、V方向2组等距离的平面与曲面相交得到的交线,通过检查曲面上的相交线来判断曲面的光顺性,对于生产的曲面光顺性分析主要有检查U、V方向的曲率梳、高亮反射线等检测方法。
高亮线分析方法可以直观地检查曲面的光顺性,通过观察线条的均匀度来判断曲面的光顺性,越均匀曲面光顺性越好。它是由1组平行光源投影到曲面上得到的1簇高光线。图13、图14为车身几个主要大面的光顺性检查结果。
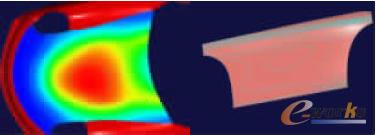
图13 车头引擎盖和车身侧面反射线分布图
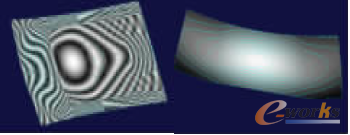
图14 车顶和车身后围板反射线分布图
可以看出:反射线分布比较均匀,曲面的光顺性基本满足要求。所以该逆向设计总体符合设计要求。
4. 结论
本文基于逆向工程技术对汽车车身进行三维造型设计研究,主要研究成果如下:1)利用Geomagic Wrap(原Studio)软件对用3D测量仪测取的点云数据进行了处理,获得拼接后的整车车身点云数据;再利用软件进行了由点—线—面的曲面重构,获得整车车身曲面模型;2)对重构的整车车身曲面模型进行连续性、光顺性分析,最终得到符合设计要求的车身CAD模型,该模型可为后续的有限元分析优化设计以及多体动力学等分析提供基础。
从目前来看,逆向工程这项技术依然存在一些发展瓶颈,从而减缓了逆向工程的发展。但是相比正向设计,逆向设计的优点很明显,能给企业带来巨大的效益,所以具有广阔的发展前景。